Pharma: The Bitter Taste of Its Medicine
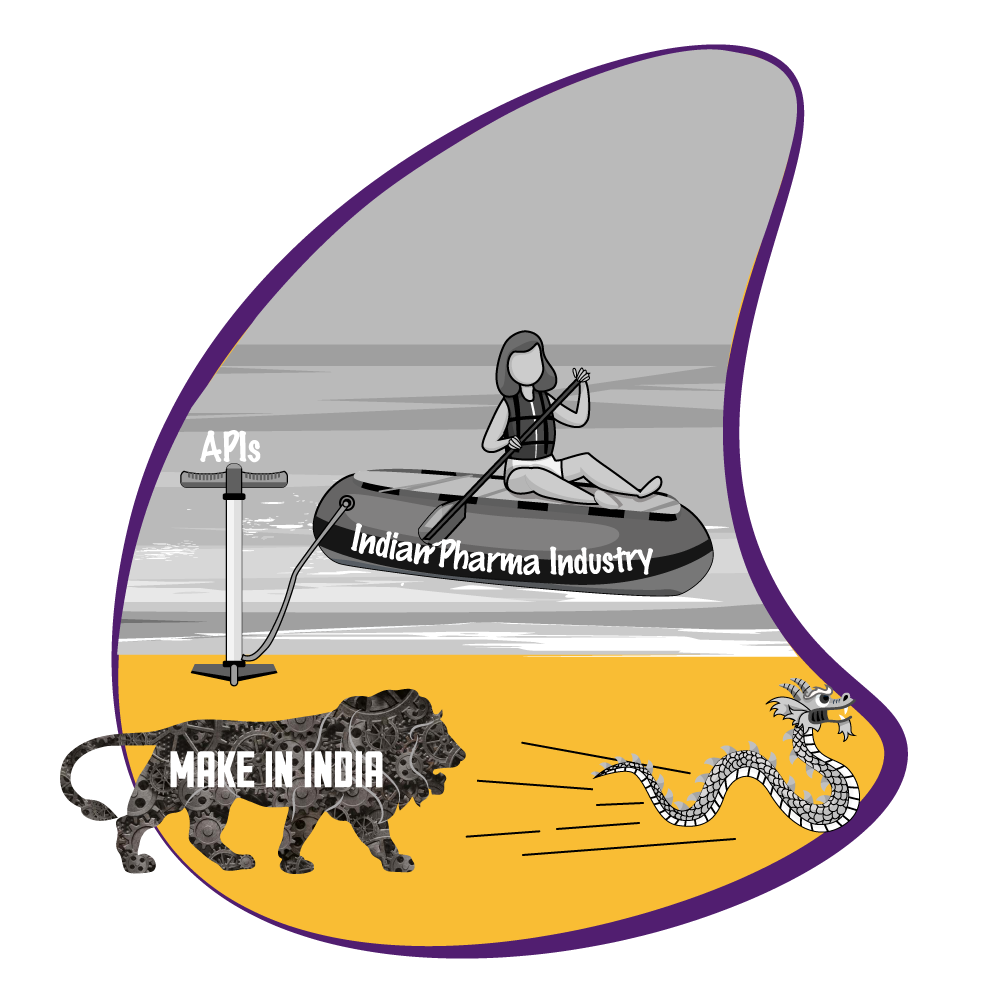
The Covid19 pandemic impacted industries all over the world. The pharma industry was no exception. In fact, in 2021, input costs in the pharma industry have seen such a steep increase that drug manufacturers, especially in the small and medium space are finding it hard to survive. In light of this, an insight into the dynamics that go into manufacturing medicines / drugs.
Raw material for pharma
Manufacturing medicines / drugs involve large scale procurement of raw material – active pharmaceuticals ingredients, excipients, glass vials and packaging material.
Active pharmaceutical ingredients (API) are chemical compounds. They are the most basic raw materials required in manufacturing a medicine / drug. For example: paracetamol is the API in manufacturing Crocin tablet. It is the raw material that gives the efficacy to a medicine when the finished medicine is consumed.
Excipients are substances that interact, enhance, support and protect the quality, medicinal functionality to enable the medicine to be consumed effectively. They give it the form, shape and colour. For example: glucose, cellulose, starch. Even water is considered an excipient. It is used for in manufacturing of the final product medicine / drug as well as a cleaning agent.
While API is an active medicinal ingredient, excipient is inactive or non-medicinal component of a medicine / drug.
Vials are glass containers used to hold liquid medicines. They are used during the manufacturing / production, testing phases and packing of liquid medicines.
Packaging materials involve a gamut of material – from aluminium foil, high quality plastic / glass bottles, vials, container seals, corrugated boxes and cartons. Packaging materials are essential, from the manufacturing stage up to the stage of the end consumer.
Source of raw material for India
China has been the largest producer of APIs. USA procures majority of its API either directly from China or from India which in turn sources it from China. Besides, this, India requires raw materials such as APIs, excipients etc. for its own production. In 2020, India imported more than 70% of APIs from China. Though India has its own API production, it is not significant. It has always depended on other countries mainly China for its requirement.
Covid 19 and its impact on the Indian pharma
The onset of Covid19 in 2020 disrupted the logistics, supply chain management around the world. Companies not only suffered halt in operations, but also struggled to procure raw materials. Similarly, complete lockdowns and halting of operations in China resulted in lesser APIs being exported to India and other countries. The pandemic coupled with the escalating political tensions (in Galwan valley) further strained the relationship with China. This severely impacted the exports from China of APIs. India which is the largest supplier of medicines / drugs to the rest of the world, struggled to procure basic raw materials due to over dependence on China and the adverse impact of Covid19.
Why the steep rise in input costs?
The APIs, excipients and packaging materials are estimated to account for almost 65% of the manufacturer’s cost. Prices of packaging material like corrugated boxes, aluminium foil has also increased by 25%-30%. China had an edge as procuring bulk APIs from China was almost 20% cheaper than manufacturing it indigenously back home. China enjoyed favourable regulatory policies, government finance incentives and economies of scale. India’s tough regulations did not give it that edge. As a result, input costs of pharma rose steeply especially in the last year or so. It was widely reported that paracetamol which was once procured at Rs. 300 per kg now costs almost Rs. 1,000 per kg. The rates have near tripled.
Impact on the Indian pharma
The pharma industry is taking the brunt of substantial increase in input costs. While the pharmaceutical giants have been absorbing such costs, the small and medium sized enterprises are finding it extremely hard to cope. Recently, the Himachal Drug Manufacurer’s Association wrote to the Prime Minister seeking government’s intervention in regulating prices of all raw materials involved in manufacturing medicines/ drugs. They also sought establishing a task force to monitor and safeguard interests of pharmaceutical companies particularly the smaller ones. Large domestic players are strengthening their production and trying to reach out to smaller companies by supplying to them indigenously. Though, this may not completely reduce dependence on China, at least it will make it reasonably independent.
The common man’s woes
Pharmaceutical giants have indicated that if the inputs costs continue to soar, then they will have to be ultimately transferred to the consumer -by increasing prices of the final medicines / drugs sold. This would be detrimental to the common man whose medical consumption is consistent irrespective of the pandemic.
Government response / action
Over dependence on China proved costly (literally) for India. In January 2021, the Central government sanctioned funds and announced the setting up of three bulk drug parks in Himachal Pradesh to manufacture APIs. The government seeks to create common infrastructure facilities. This has been done with the intention of reducing dependence on China. Besides becoming independent from China, the bulk drugs parks aim to generate employment and strengthen the economy. This is in line with the “Make in India” initiative of the present government. Several other States have shown interest in setting up such bulk drug parks in their respective States. If that happens, in the next few years, India will become substantially self-reliant.
A proactive approach by the government at the centre and states coupled with ease of doing business policies is key to regaining India’s status as the pharmacy of the world.